CAPABILITIES
Transfer Die Stamping
Transfer press stamping has evolved to meet the growing demand for high-volume, intricate metal components. With single-stroke stamping, complex components can be expensive and labor-intensive, requiring technicians to manually reposition parts at multiple presses. Instead, transfer press stamping automates multiple operations, making it easier to create detailed metal parts. Today transfer press components make up auto parts, light fixtures, HVAC systems, aerospace products, and more.
What is the Transfer Press Stamping Process?
- Piercing
- Beading
- Bulging
- Coining
- Curling
- Extruding
- Notching
- Threading
Transfer Presses vs. Progressive Die Presses
Features of Transfer Press Stamping
In transfer press stamping, a single press operates multiple stamping stations at once. The first station forms individual blanks, which are transferred and repositioned freely between stations. Automated mechanical transfer mechanisms move the workpieces, streamlining complex operations into a single process.Features of Progressive Die Presses
In progressive die stamping, a metal workpiece is fed through the machine, which performs one or more stamping operations at each station until the part is complete. A metal coil advances multiple workpieces through the workstations as one, until the final station separates the individual workpieces. Progressive die stamping tools feature more complex geometries and result in quicker production.Benefits of Transfer Press Stamping
Compared to progressive die stamping, transfer press stamping is more cost-effective and versatile, especially for short production runs. It is also ideal for producing large parts with specialized features. Since workpieces are separate from the raw coil, transfer press stamping can shape individual components completely over the course of one stamping cycle, eliminating the need for additional processing.Benefits of Progressive Die Presses
Generally, progressive die stamping is quick to set up and cost-effective for long production runs. The process is highly efficient and repeatable, creating consistent components with tight tolerances. It also generates less material waste. For these reasons, progressive die stamping is best for productions requiring high volumes in a short period of time.Transfer Press Types
Trans-Matic is equipped with 119 transfer presses whose tonnage ranges from 5 to 600 tons. This range allows us to select the ideal press for components of different sizes and shapes.
Our presses consist of Individual Cam Operated Plungers (ICOP) and Solid Bed “Die Set” models. Both types of press enable fast and reliable production at low operating costs.
- Individual Cam Operated Plungers (ICOP): A single ICOP acts like multiple presses in one. Each station moves independently from the others, but the integrated transfer mechanism synchronizes their individual operations. This press enables easy customization throughout each production run.
- Solid Bed “Die Set” Press: Like an ICOP, a solid bed press features independent but synchronized press stations. Instead of using a rotary mechanism, a solid bed press has a flat surface that initiates the press motion and activates multiple stations simultaneously.
Advantages of Transfer Press Stamping
- Best for producing large components
- Broad setup flexibility
- Cost-effective for short, mass production runs
- Low tooling costs
- Simple operation
Trans-Matic’s Transfer Press Capabilities
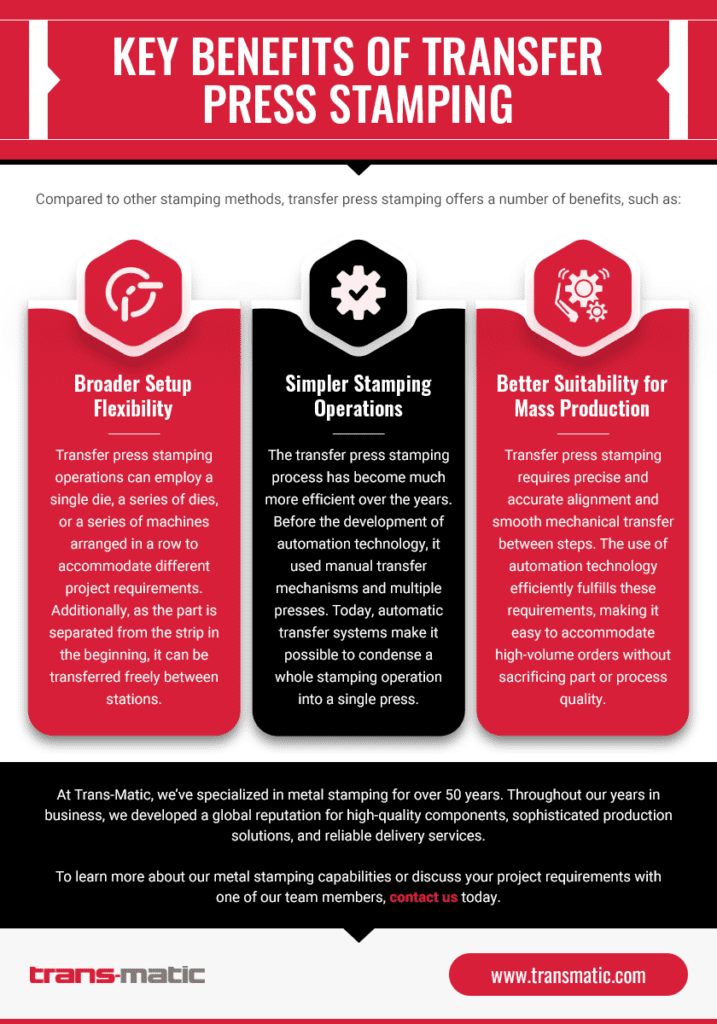
GET IN TOUCH
Contact us for your next project
We’ve been perfecting our deep draw forming processes since 1968, and have the skills and experience to deliver the high quality, high precision deep draw parts you need. Contact Trans-Matic to get our team started on your deep draw stamping project.